こんなものがあったら。あんなことができたら。夢を夢で終わらせないのが研究者。夢の実現のために、日々研究に取り組んでいる人たちが日産にはたくさんいます。
今回は、日産の若手研究者と、彼らが働く総合研究所をご紹介します。クルマ会社の研究者とは、いったいどんな人たちなのでしょうか?

いざ総合研究所へ!
日産の総合研究所は、神奈川県の厚木市と横須賀市にあります。なかでも、横須賀市追浜にある一番古い建物は、1958年より日産の研究施設として使われています。最先端の技術が歴史的な建物の中で研究されていると思うと、ちょっと驚いてしまいますね。

総合研究所ってどんなところ?
日産では、多くの技術開発が総合研究所から始まります。ここで行われているのは、10年以上先に必要とされる技術の研究。世の中の動向をとらえ、将来のニーズを正しく分析し、先行開発やその先の実用化につなげるために、4つの領域に注力し研究を重ねています。
- カーボンニュートラルに向けた「電動化の推進」
- 新たな移動の価値を生み出す「モビリティサービスの発展」
- クルマに加え、開発、生産の知能化も支える「AI活用領域の拡大」
- 未来のクルマをつくる「生産技術の革新」
日産の進むべき道を示す「羅針盤」の役割を担う総合研究所。
そこには、「まだだれも見たことのない、新しい価値を持つ技術で世の中を変えたい!」と情熱を燃やす研究者たちが集まっています。
研究者へ突撃インタビュー
その中でも、注目分野で研究を続ける若手研究員に話を聞いてみました。
ミクロの世界で夢の粉をつくり出す!
3Dプリンター 目片萌絵(3年目)
クルマづくりの常識を塗り替える3Dプリンター技術。それは、カーボンニュートラルを目指す上でも、重要な鍵を握ります。ものづくりに魅了された入社3年目の目片が、ミクロの世界に挑む情熱を語りました。
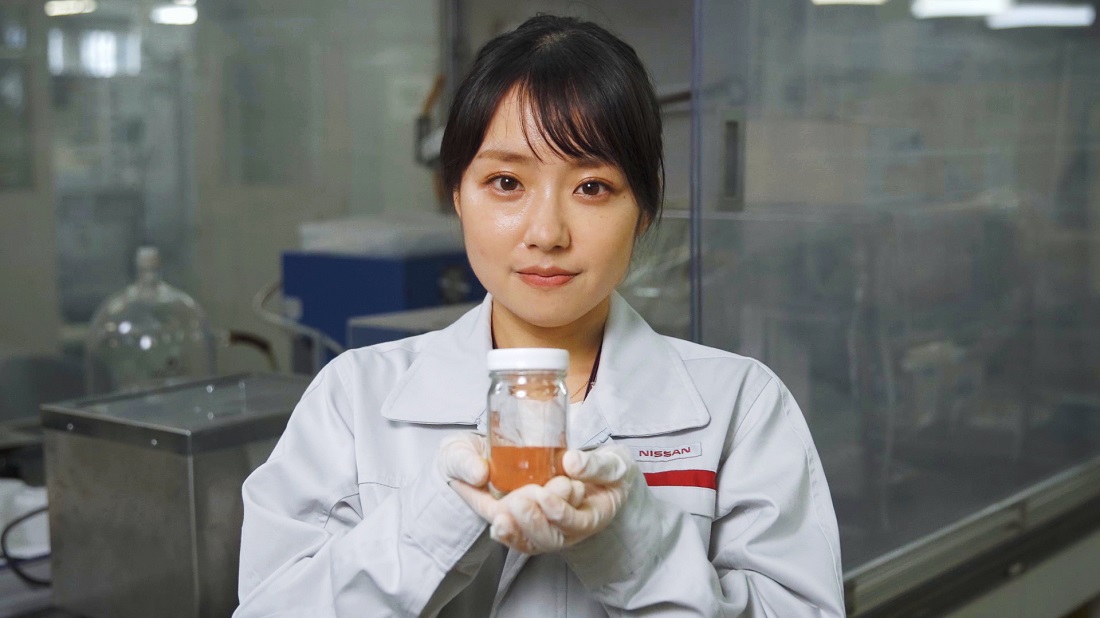
「3Dプリンターで金属部品をつくると、クルマづくりの世界が変わります。なぜなら、金型が不要で、データさえあれば自由な形状の部品が成型できるからです。複数の部品を一体で成型できるので、軽量化できます。さらに、一つの部品で、ここは硬く、ここは柔らかく、というように、部位によって強度を変える。あるいは、ここはアルミ、ここは鉄、というように求められる性能に応じて素材を変える。そういった夢のようなことができるようになるのです。エンジニアなら誰もが欲しいと願う、理想の部品がつくれるようになります。」と目片は目を輝かせます。
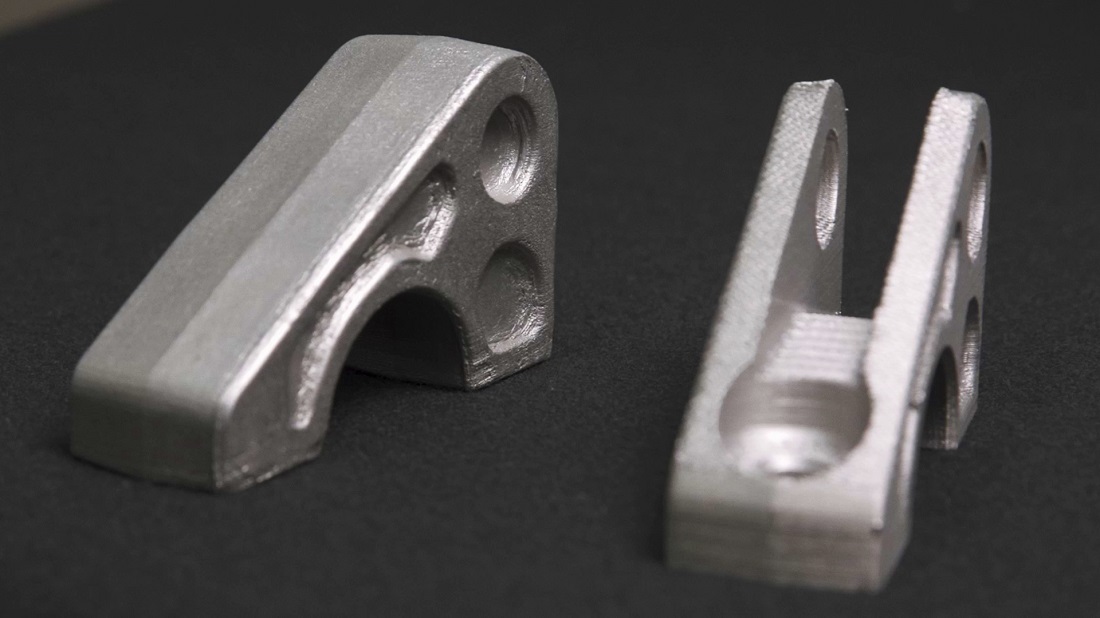
この3Dプリンターで材料となるのは、金属の粉末です。この粉末を一粒一粒、層を重ねるように積み上げ、一体成型していきます。これまでの鋳造や切削、溶接によって部品を生成する方法とは異なり、必要な部品だけを無駄なくつくることができるようになります。目片は、この金属粉末の開発を担当しています。3Dプリンターでつくった部品を市販車へ適用するためには、材料である粉末の高品質化と低コスト化が求められます。
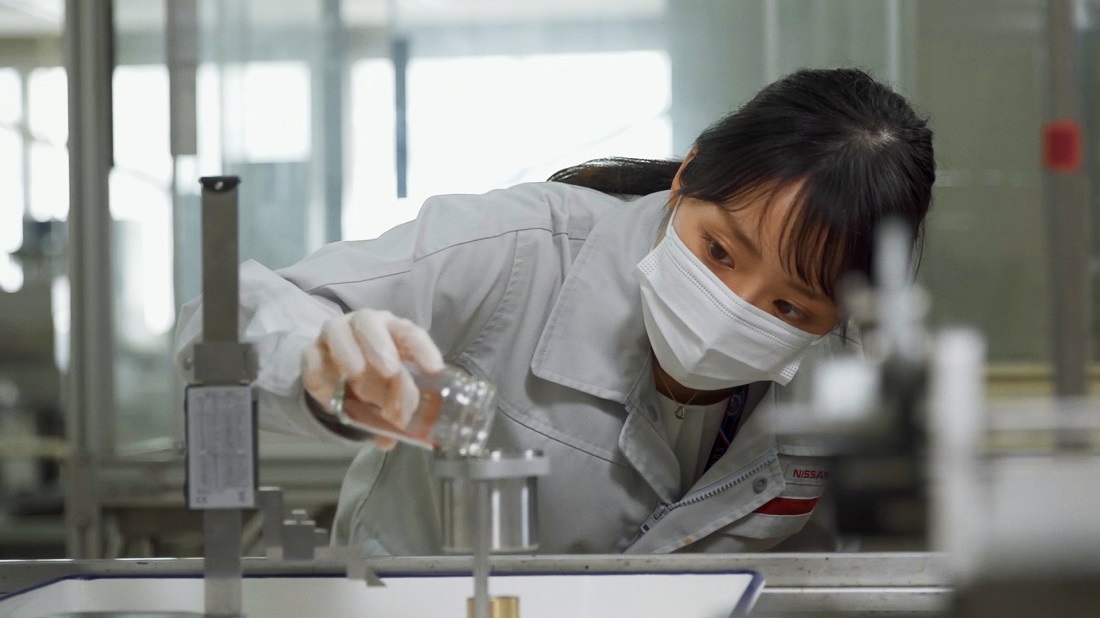
3Dプリンターへの注目が高まっているのは、自由度が高く、効率的な成型が可能だからというだけではありません。カーボンニュートラルの実現に向けた日産の取り組みにおいても、重要な役割のひとつを担っています。電動車両は環境負荷が少ない一方で、電池を搭載するため、車両重量が重くなる傾向にあります。しかし、3Dプリンターでつくった部品を使えば車両の軽量化に貢献でき、航続距離を伸ばすことが期待できるのです。また、これまで別々に製造していた部品を一体化し、形状を最適化することで、工程を集約し、材料を削減することも可能になります。


学生時代から数ミクロン単位の世界で生産技術の研究をしていた目片は、数ある製造業の中でも「より裾野の広いものづくりができるクルマの生産に関わりたい!」と日産に入社しました。
「3Dプリンターでつくる部品の最終的な性能を決めるのは、粉末一粒一粒の品質です。だからこそ、まだ誰も実用化していない新しい粉末、そして最高品質の粉末の開発を目指しています。」
毎日、粉と向き合っている目片は、朝起きてコーヒーを飲むときにも「このフィルターの目の粗さなら、私のつくった金属粉末が通過できる。」とつい考えてしまうそうです。例えば、髪の毛の太さは約50~100µmですが、目片が向き合っているのは、さらに細かい10μm~50μmの粉末。ミクロの世界で理想の粉末を追い求め、日々奮闘しています。
「EVのさらなる普及へ」 力をあわせてブレークスルーを起こそう!
全固体電池 川上裕貴(7年目)、吉野和宙(4年目)
次世代電池として注目を集める全固体電池。川上はアメリカのパデュー大学で世界中から集まった研究者や学生たちと。吉野は日産の先輩研究者たちと。場所は離れていても思いは一つ。二人は、全固体電池を実用化するためのブレークスルーを求め、ともに奮闘しています。

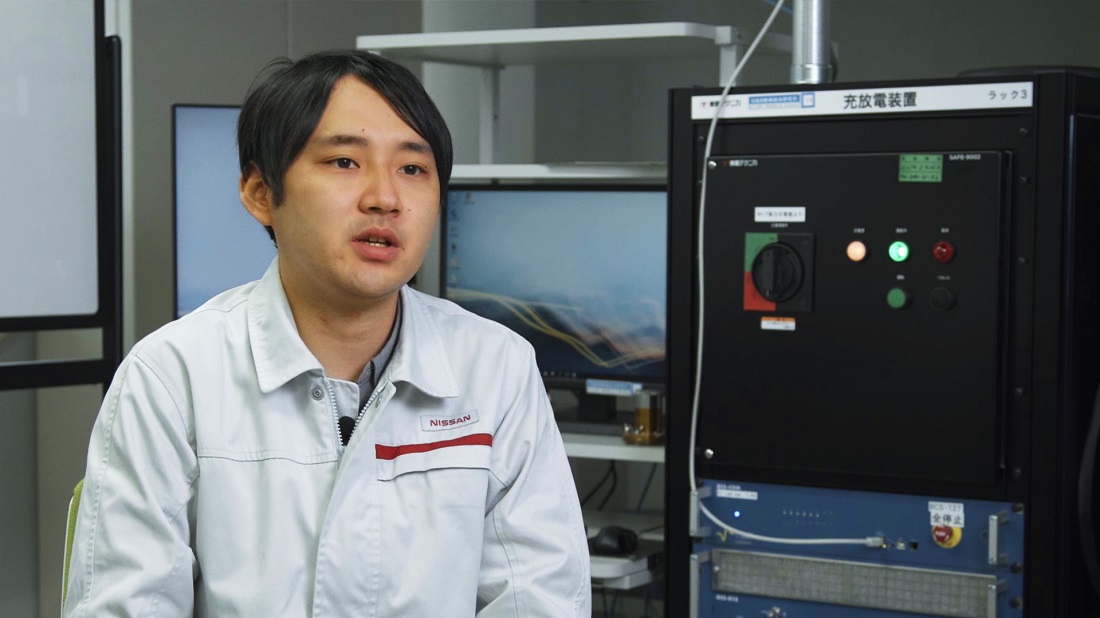
多くの電気自動車(以下、EV)で使用されているリチウムイオン電池は、リチウムイオンを通す電解質が液体です。これに対して、全固体リチウムイオン電池(以下、全固体電池)の電解質は固体。なぜ、この全固体電池が今注目されているのでしょうか。総合研究所の若手研究員の二人に話を聞いてみましょう。
「全固体電池の最大のメリットは、エネルギー密度の大幅な向上です。電極の材料を、従来よりも多くのエネルギーを蓄えられる物質に置き換えることで、現行のリチウムイオン電池と比べ、より小さな体積でより大きなエネルギーを使用できるようになるのです。」と吉野は熱く語ります。「これがEVに搭載されれば、航続距離を飛躍的に伸ばすことができると期待されています。」
さらに、電解質が液体から固体になることで、より速く充電することが可能になるともいわれています。より長い距離を走るための電気を、より短い充電時間で充電できるようになると見込まれる全固体電池は、まさに、EV普及を加速させるキープレイヤーなのです。
全固体電池の実用化に向け、総合研究所の吉野は、日々いろいろな条件で設計した電池を試作し、目標性能が発揮できているかどうか確認するための実験を行っています。一方、川上は全固体電池のさらなる可能性を追求するため、日産の若手研究者を対象とした海外派遣プログラムに参加し、現在アメリカのパデュー大学に在籍しています。大学では他の研究者たちと、「電池の内部で何が起きているのか」「どのような性能が実現しうるのか」を調べるためにシミュレーションを繰り返し、その結果をもとに総合研究所で実験を行う電池の設計を提案します。
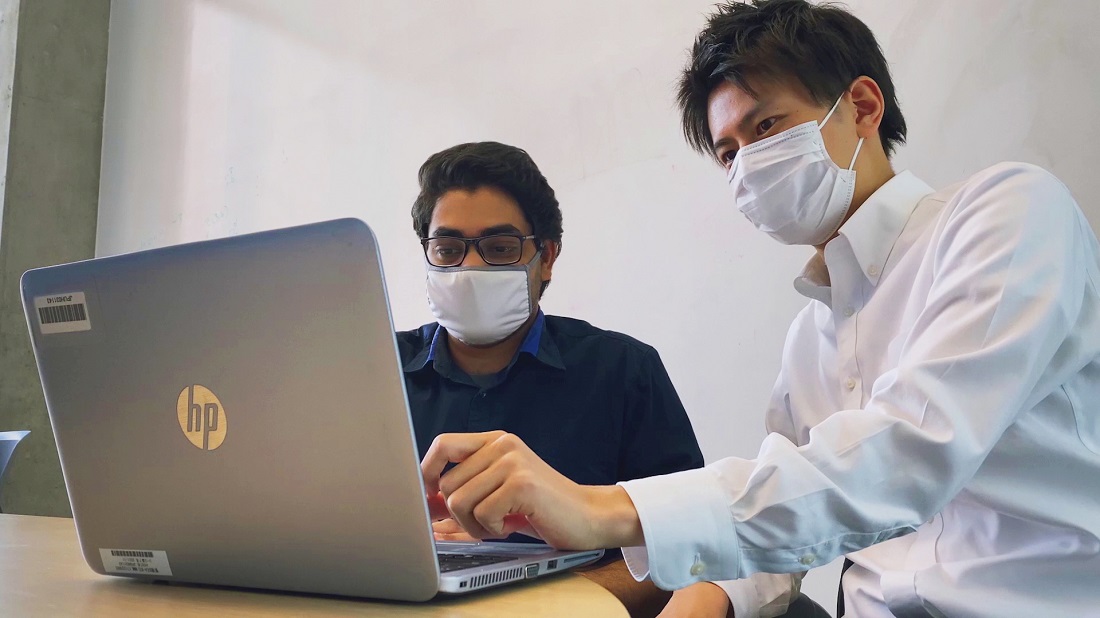
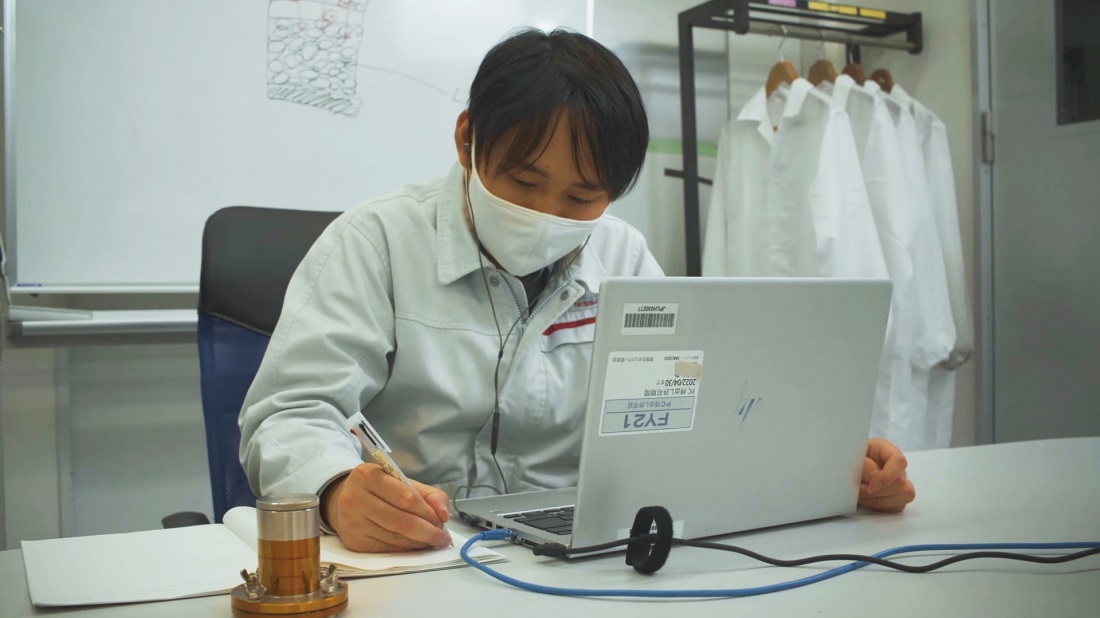
このように日米で昼夜研究を重ねている全固体電池ですが、実用化に向けて、どのようなブレークスルーが必要になるのでしょうか。
「全固体電池の開発で特に難しいことの一つは、電極でリチウムイオンを蓄える活物質という粒と、リチウムイオンを通す電解質の粒を密着させることです。」と川上は語ります。
「話が難しいですよね。では、例を挙げます。缶ジュースは、氷だけを入れたバケツに入れるよりも、氷水を入れたバケツに入れたほうが冷えやすくなります。前者は缶と氷が点でしか触れていないので熱が伝わりにくいのですが、後者の場合、缶と氷水が面で触れるので、効率的に冷やすことができるのです。電池も、電解質が液体の場合は、電極の活物質とぴったり接することができます。しかし、固体電解質の場合、固体同士の接触となるので隙間が生まれやすく、活物質と電解質の間をリチウムイオンが通りにくくなってしまうのです。そうすると、電池を使用したときに、エネルギーの損失が大きくなってしまいます。」

「より密着させるためには、外側から高い圧力をかける装置が必要になります。しかし、せっかくエネルギー密度を高めて小型化した電池に、圧力をかけるために大きな装置を装着するのでは意味がありません。低い圧力で、いかに電極の活物質と電解質を十分に接触できるようにするかが、このジレンマを解消する鍵で、日々試行錯誤を続けています。」
解決すべき課題がまだまだ多くある分野ですが、二人は前向きに研究に向き合っています。
川上は、「電池内部で何が起こっているのか、まだわからないことも多いんです。起きている現象をより深く理解するためには、解くべき課題も多い。難しい課題について、文化や考え方が異なる現地の研究者や学生たちと日々議論し、お互いの意見を摺り合わせていく。難しいからこそ、課題解決のために全員の足並みが揃った瞬間はたまりませんね。」と目を輝かせます。
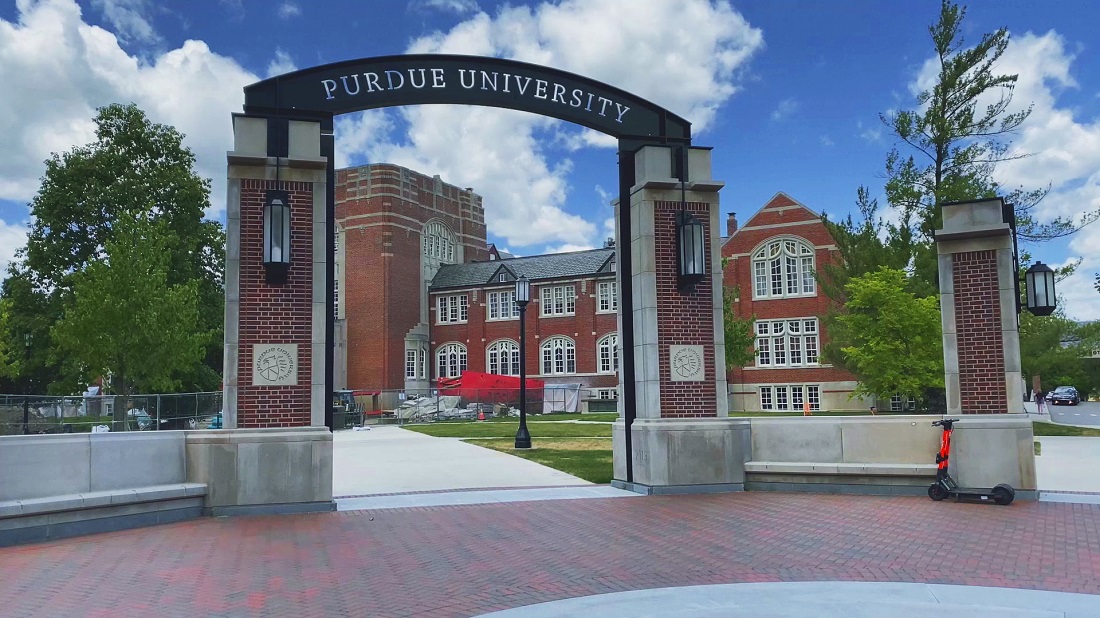
一方、学生時代から全固体電池の研究に携わってきた吉野は、「若手の意見を聞いて、自由にやらせてくれるのが日産の良いところだと思います。同年代の仲間も多いので、お互いに切磋琢磨しながら電池と向き合っています。試行錯誤を繰り返す中で、狙った通りの性能が確認できた時は、思わずガッツポーズをしてしまいます」と語ります。
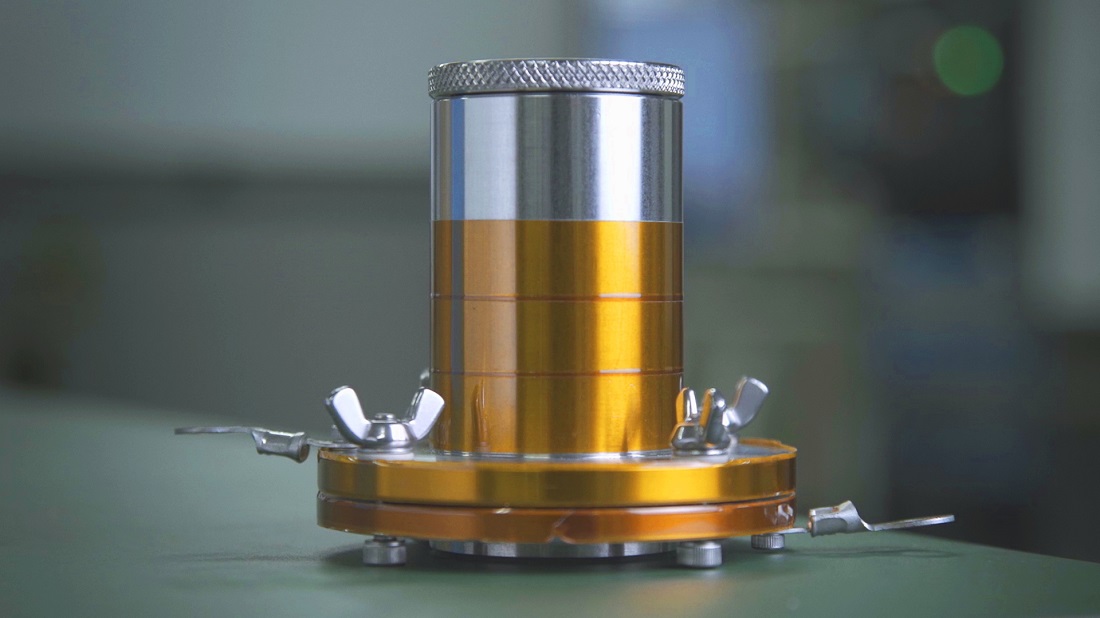
ところで、電池研究者ならではのこだわりが、二人の日常生活に影響することも。
川上がスマートフォンのバッテリーを長持ちさせるために、普段からしていることは何だかわかりますか?熱を逃がすため、スマートフォンは必ずアルミ箔の上に置くこと、だとか。吉野は、日常的に材料を細かく均一に混ぜ合わせる作業を行っています。そのため、とんかつ屋で胡麻をすり鉢に入れた瞬間、ついスイッチが入ってしまうそう。
強いこだわりを持つ二人の若手研究者は、EV搭載用の全固体電池の実用化に向けて尽力しています。
日産には、こうした情熱あふれる若い研究者がたくさんいます。創業以来大切にしてきた「他がやらぬことをやる」の精神を胸に、彼らは、今日もお客さまに未来の技術を届けるための研究を続けています。